As gravitational waves move through spacetime, they stretch it and contract it along orthogonal directions, much like a rubber sheet that when stretched along one axis, contracts along the normal axis. LIGO measures these waves with an interferometer — an L-shaped detector with 2 orthogonal 4-km-long arms. Laser light emitted from the vertex, travels down the arms, and reflects back from the end mirrors. The time difference between the 2 returning beams gives the arm-length difference — the gravitational wave signal. At present, LIGO can detect arm length differences of 10-19 m, or one billionth of an atom. To achieve this incredible sensitivity, LIGO requires the world’s most stable laser and its highest quality mirrors, because minimizing the noise in the reflection process is truly where “the rubber meets the road” for gravitational wave detection.
Precision Optical Metrology describes our research on the test mass mirrors and related optical and suspension systems. Syracuse has been an international leader in this research for over 25 years. (Link to the history section)
Mirror Substrates: LIGO’s test mass mirrors are thick cylinders (35 cm OD × 15 cm) of fused silica, an extremely pure form of glass. At SU, we developed the method for minimizing the noise in fused silica, and now this low loss material is used in the mirror substrates, the suspension fibers, the mirror coatings, and almost every device where low thermal noise is a requirement. Materials with low thermal noise have low dissipation, or energy loss. We also say that they have high quality because they loose energy very slowly (and they ring with a very pure tone, or narrow resonance). Our lab performed the highest-ever measurement of the fused silica quality factor. Once we brought our sample to resonance, it rang for a week while the amplitude fell to only 1/5 of the original value!
Mirror Coatings: The thermal noise in LIGO’s mirrors is, somewhat surprisingly, due primarily to the few micron thick mirror coating, rather than the 15 cm thick substrate. In 1998, Yuri Levin calculated that LIGO may be limited by high levels of this coating thermal noise. That noise was first measured in our SU lab the next year, confirming Levin prediction. With our colleagues at Glasgow and Stanford, we isolated the source of the noise by 2003, and by 2007 had developed the lower noise coatings now used in Advanced LIGO. These mirror coatings have allowed us to detect gravitational waves, but to see further into the universe requires coatings with much lower noise.
We have continued to explore amorphous metal-oxide materials, like those used for Advanced LIGO, to develop a better mirror coating. However, this research path has thus far yielded only minor improvements over many years.
Several years ago we began a project with Garrett Cole of Crystalline Mirror Solutions to develop crystalline mirrors for LIGO. Cole produced small mirrors made from a single crystal with alternating high and low index layers of gallium arsenide (GaAs) and aluminum gallium arsenide (AlGaAs). The bare crystal had very low thermal noise, but it required years of research to produce larger coatings with that same low noise. We are now making 10-cm coatings with 10× lower noise than the Advanced LIGO coatings. Our goal is to expand to 20-cm coatings and then 30-cm coatings, which are usable for LIGO.
We have facilities for measuring room temperature and cryogenic mechanical loss in coating samples.
Metrology: Our laser lab has the capability for performing various optical tests on mirror coatings. We have measured the electro-optic noise in crystalline coatings and are currently testing a new arm-length stabilization setup for crystalline coatings. We were recently funded for a new experiment to measure birefringence noise in crystalline coatings.
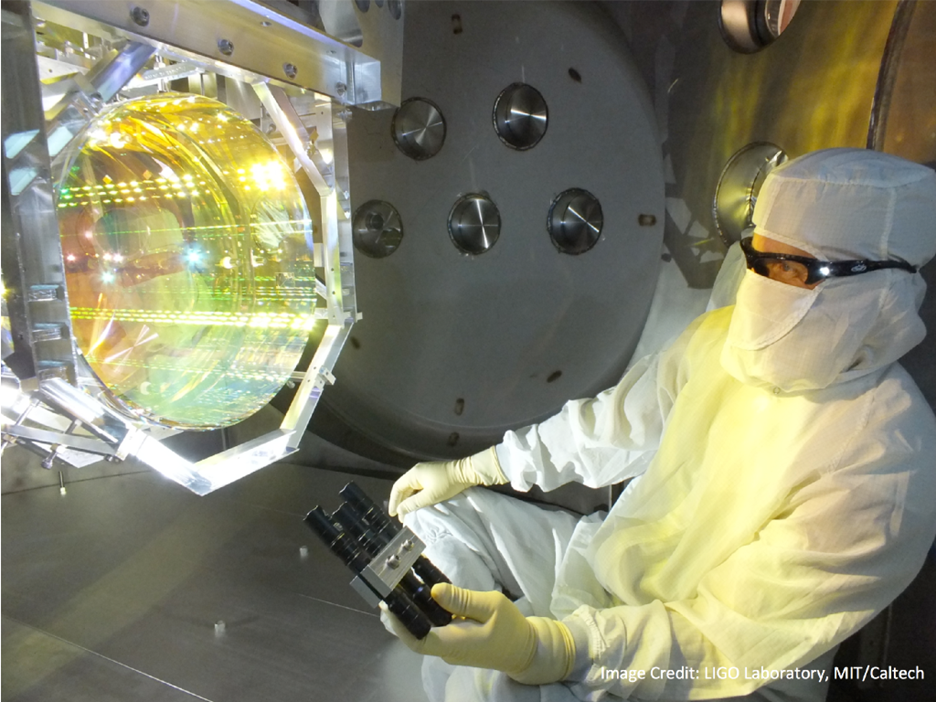